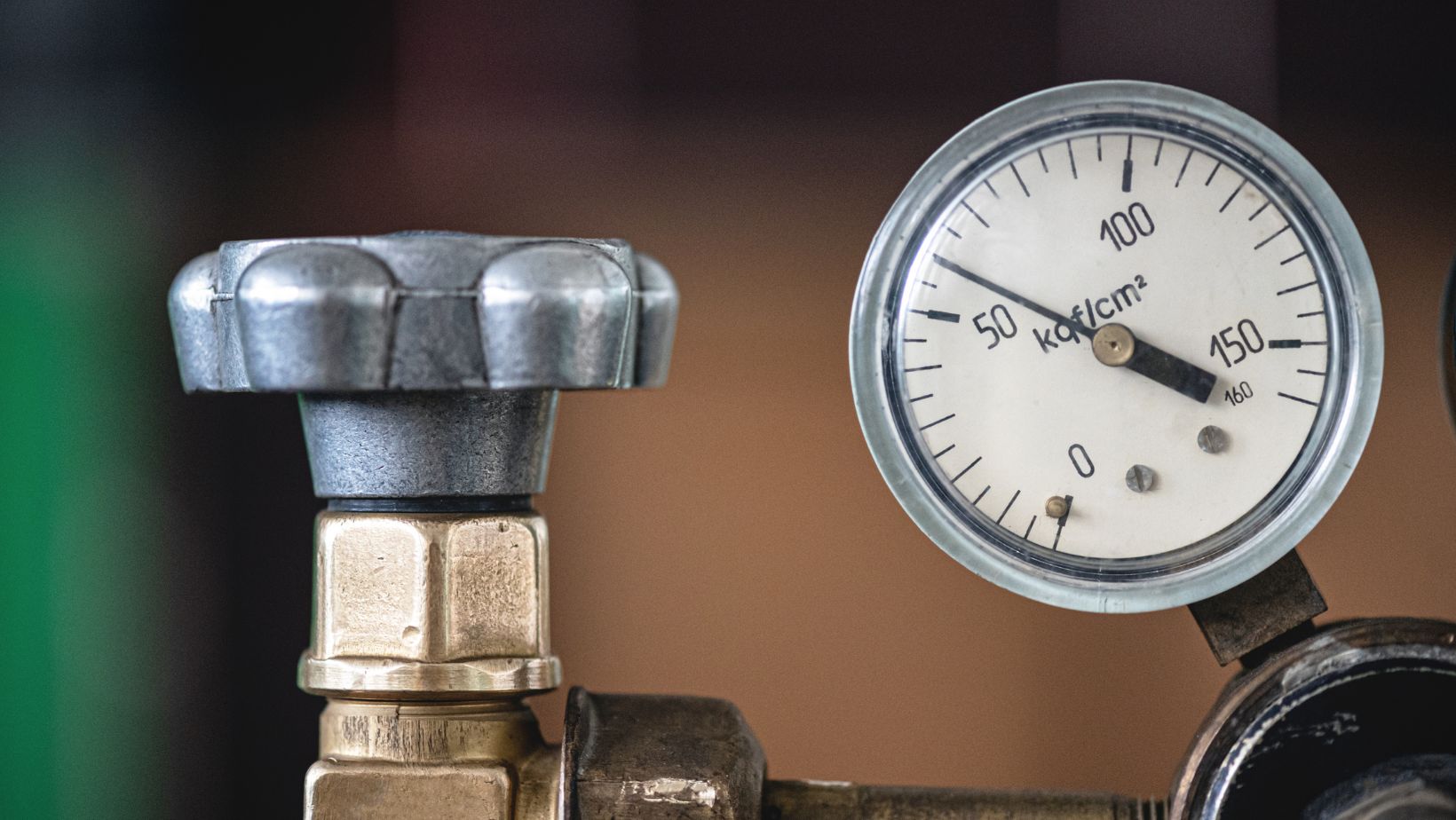
Introduction
Concrete is one of the most versatile and widely used construction materials in the world. Its strength, durability, and ability to be molded into various shapes make it ideal for countless applications. However, the quality of concrete depends significantly on its composition and the processes involved in its creation and testing. One crucial aspect of concrete quality is its air content, which is where the concrete air meter comes into play. This comprehensive essay explores the importance, function, types, operation, and implications of the concrete air meter in the construction industry.
Importance of Air Content in Concrete
Air content in concrete refers to the volume of air voids within the hardened concrete mix. These voids can be either entrapped air or intentionally entrained air. Entrapped air occurs naturally during the mixing process, whereas entrained air is deliberately introduced using air-entraining agents. The primary reasons for controlling air content in concrete include:
- Durability: Air-entrained concrete is more resistant to freeze-thaw cycles, which can cause cracking and deterioration in non-air-entrained concrete. The microscopic air bubbles provide pressure relief during freezing, preventing internal stresses.
- Workability: Proper air content improves the workability of concrete, making it easier to place and finish. This is particularly beneficial in large-scale projects.
- Strength: While excessive air content can reduce the strength of concrete, the right amount of air can balance durability and strength. This balance is crucial for structural integrity.
- Resistance to Chemical Attack: Air-entrained concrete is more resistant to sulfate attack and other chemical reactions that can degrade concrete over time.
Function of the Concrete Air Meter
The concrete air meter is an essential tool used to measure the air content in freshly mixed concrete. Accurate measurement of air content ensures that the concrete mix meets the specified requirements for a given project. The primary functions of the concrete air meter are:
- Quality Control: Ensures the concrete mix meets the design specifications, enhancing the longevity and performance of the structure.
- Compliance: Helps in complying with industry standards and regulations, such as those set by ASTM (American Society for Testing and Materials) and AASHTO (American Association of State Highway and Transportation Officials).
- Troubleshooting: Identifies issues in the mix that could affect the final product, allowing for adjustments before the concrete is poured.
Types of Concrete Air Meters
There are several types of concrete air meters, each suited to different testing requirements and standards. The most commonly used types include:
- Pressure Method Air Meter (Type B Meter): The most widely used type, particularly in the United States. It operates based on Boyle’s Law, which states that the pressure of a gas is inversely proportional to its volume. This method involves filling the meter with a concrete sample, applying pressure, and measuring the change in volume to determine air content.
- Volumetric Method Air Meter (Roll-a-Meter): Commonly used when lightweight aggregates are present. This method involves agitating the concrete sample in a container filled with water and measuring the volume of displaced air. It’s known for its accuracy but is more time-consuming compared to the pressure method.
- Gravimetric Method: This method involves measuring the weight of a known volume of concrete before and after air is removed, typically using a vacuum. It is highly accurate but less commonly used due to its complexity and the need for specialized equipment.
Operation of a Pressure Method Air Meter
The pressure method air meter is the most common and will be discussed in detail. Here’s a step-by-step guide on how it operates:
Equipment and Materials
- Pressure air meter
- Concrete sample
- Tamping rod
- Mallet
- Scoop
- Water
Procedure
- Preparation: Assemble the air meter, ensuring all components are clean and in good working condition. Dampen the interior surfaces to minimize absorption.
- Filling the Meter: Fill the measuring bowl with the concrete sample in three layers, each approximately one-third of the volume. Compact each layer using the tamping rod, applying 25 strokes per layer to eliminate air pockets.
- Leveling the Surface: Strike off the excess concrete to achieve a level surface with the rim of the bowl. Clean the rim to ensure a proper seal.
- Assembling the Lid: Attach the lid of the air meter, ensuring a tight seal. Fill the air chamber with water to eliminate any air gaps.
- Applying Pressure: Close the air bleeder valve and pump air into the chamber until the gauge reads the initial pressure line. Close the air pump valves.
- Releasing Pressure: Open the air bleeder valve slowly. The pressure drop will indicate the air content in the concrete. The gauge reading corresponds to the percentage of air in the sample.
- Recording Results: Record the air content and any observations about the concrete sample, such as workability or anomalies.
Calibration and Maintenance
Accurate air content measurement relies on proper calibration and maintenance of the air meter. Regular calibration ensures the meter provides reliable results. The following steps outline calibration and maintenance procedures:
- Calibration: Conduct calibration checks using a calibration cylinder and known volumes of air. Adjust the meter as needed to ensure accuracy.
- Cleaning: Thoroughly clean the meter after each use to prevent residue build-up, which can affect readings.
- Inspection: Regularly inspect seals, valves, and the pressure gauge for wear or damage. Replace components as necessary.
- Storage: Store the air meter in a dry, protected environment to prevent corrosion and damage.
Implications of Air Content Testing
Accurate air content testing has several critical implications for construction projects:
- Structural Integrity: Ensures the concrete mix meets design specifications, contributing to the overall strength and stability of the structure.
- Longevity: Air-entrained concrete is more durable, particularly in harsh weather conditions, extending the lifespan of structures.
- Cost Efficiency: Prevents costly repairs and maintenance by ensuring the initial quality of the concrete mix.
- Safety: Reduces the risk of structural failures, enhancing the safety of buildings, bridges, and other concrete structures.
Conclusion
The concrete air meter is an indispensable tool in the construction industry, providing crucial data on the air content of freshly mixed concrete. Understanding its operation, types, and the significance of accurate air content measurement helps ensure the quality and durability of concrete structures. By implementing regular calibration and maintenance procedures, construction professionals can rely on concrete air meters to deliver consistent, reliable results, ultimately contributing to the safety and longevity of our built environment.
In summary, the concrete air meter plays a pivotal role in modern construction, from quality control and compliance to troubleshooting and safety. Its accurate measurement of air content in concrete helps achieve the delicate balance between durability, strength, and workability, ensuring that concrete structures can withstand the test of time and environmental challenges. As technology and standards evolve, the concrete air meter will continue to be a cornerstone of concrete quality assurance in the construction industry.