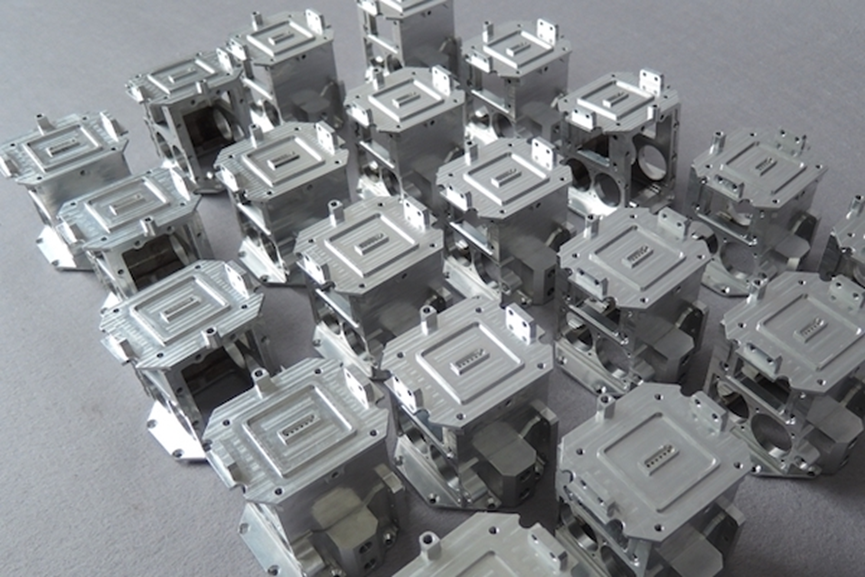
The complexity of the internal structure of thin-walled parts, as well as its relatively low stiffness, will cause deformation that can easily occur during CNC machining. At this stage, CNC machining services are often used for the machining, processing, and production of thin-walled parts. This results in a series of problems such as uneven thickness up and down the thin wall as well as inappropriate size, more or less than the expected target, making the overall quality of thin-walled parts decline, the accuracy can not meet the requirements of aerospace, medical equipment and other fields.
Considerations for Machining Thin-Walled Aluminum Alloy Parts
According to practical experience, the machining process of thin-walled aluminum alloy parts should consider the following aspects:
Cutting speed
Cutting speed has a great influence on the possibility of plastic deformation of thin-walled aluminum alloy parts. Both too high and too low cutting speeds can lead to deformation. Selecting an appropriate cutting speed helps prevent deformation and improve surface smoothness in CNC machining services. Therefore, the cutting speed should be determined according to the actual machining needs.
Geometry
The potential deformation of thin-walled aluminum alloy parts varies with their geometry. Even if the cutting speed is the same, different types of tools can affect the machining results of thin-walled aluminum alloy parts.
Feed rate and depth of cut
Changing the feed rate and depth of cut during machining will alter the cutting force, which will cause deformation of aluminum alloy thin-walled parts. Therefore, in the machining process, it’s crucial to strictly control feed rate variations. In addition, deformation of aluminum alloy thin-walled parts is also affected by process parameters and specific machining modes, especially in the case of changes in axial depth of cut index.
Use of fixtures
In order to ensure the stability, fixtures need to be used to fix thin-walled aluminum parts. However, when the fixture is not reasonably selected, the clamping force, gravity and inertia force on the parts can not reach a balance, causing deformation. So, controlling the parameters and types of fixtures to avoid unnecessary processing quality problems is essential.
Thin-walled parts deformation control measures
Selection of cutting fluid
Cutting fluid is one of the important materials in the machining of thin-walled aluminum parts, avoiding excessive tool wear and surface roughness. In the roughing process, due to the large tool diameter and cutting volume, the heat generated by the contact friction between the tool and the thin-walled aluminum alloy is easy to cause deformation and rapid tool wear. Therefore, the cutting fluid must be reasonably used to control the processing temperature.
Lonic cutting fluid and 3% ~ 5% emulsion can provide cooling effects. With carbide tools, which have strong heat resistance, they can be poured continuously and sufficiently to avoid problems such as uneven heat and cold caused by interrupted pouring. Reduce the possibility of cracks in the tool.
In the finishing process, the cutting fluid plays a role in reducing the surface roughness and improving the machining accuracy. For aluminum alloy parts, choosing ionic cutting fluid or 10% ~ 12% emulsion can reduce the milling force and avoid the friction power consumption generated by excessive milling force.
From practical processing experience, the more outstanding the lubricating properties of the cutting fluid, the lower the possibility of deformation of parts caused by cutting force. For example, mineral oil can make the main cutting force reduction of 12% ~ 15%, vegetable oil can reduce it by 20% ~ 25%.
Surface Protection
The hardness and strength of aluminum alloy are very low, and the surface is easily scratched during the machining process, affecting the overall shape of the thin-walled parts.
During support with a steady rest, the tightness between the bracket and the workpiece should be controlled, and ensure uniform force of the 3 jaws is consistent. Leather belts can be used to protect the surface while avoiding the deformation of thin-walled parts.
In addition, the shape of the aluminum alloy thin-walled parts also affects the machining difficulty. For long barrel-shaped parts, when machining, the weight of the tool holder’s cantilever should be considered. The machining accuracy of the aluminum alloy thin-walled parts can be ensured by setting up the counterweight toolbar to avoid the risk of unnecessary deformation.
Selection of suitable tools
The machining quality of thin-walled aluminum alloy parts is affected by a combination of factors. The cutting performance of the tool, material parameters are among the most important influencing factors. Therefore, it is necessary to reasonably select the tool to avoid unnecessary deformation of aluminum alloy thin-walled parts.
The tool is preferred to high-speed steel tools, choose a larger tool front angle, generally 15 ° is the most appropriate. Roughing cutting material should not be too large, generally choose 0.50 ~ 1.50 mm can be. Avoid cutting too large roughing stresses involved in the parts.
Optimizing Machining Sequence
In addition to the measures already mentioned above, in order to control the deformation of aluminum alloy thin-walled parts, we also need to combine the characteristics of aluminum alloy, reasonably adjust the machining sequence, and avoid the quality problems caused by irrational arrangement of the machining sequence.
First of all, it is necessary to realize the separation of rough machining and finishing. In the rough machining process, let the internal stress be released. For parts that require finishing, finishing should be carried out after a period of rough machining to release internal stress and prevent deformation.
Secondly, symmetrical machining should be performed. Avoid continuous machining on one side so as not to hinder heat dissipation. Use coolant when double-sided machining to reduce the probability of deformation.
Conclusion
According to the actual machining conditions of thin-walled aluminum parts, selecting suitable clamping methods, tools, cutting parameters, cutting fluid types and machining processes can effectively reduce the deformation during CNC machining. This method can improve the machining efficiency and product qualification rate.